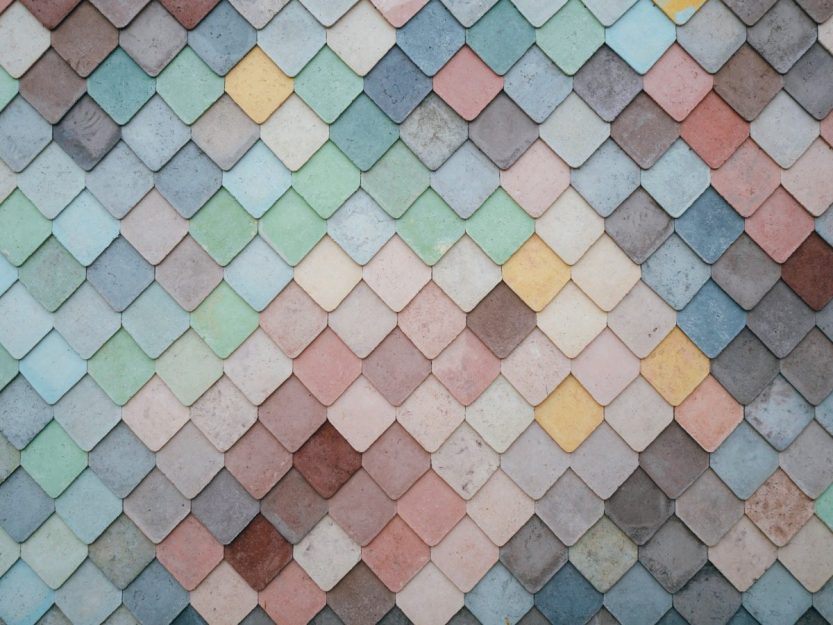
25 Oct Best Available Technologies for Reducing Resources’ Demand: Pre-treatment and Dyeing with Reactive Dyes
Pre-treatment & Dyeing with Reactive Dyes-Ulrich Hanxleden
As a mosaic starts with a first stone, textile finishing starts with Pre-treatment
A mosaic is the assembly of separate tiny stones or other materials in order to create an image. As each small stone contributes to the overall aesthetic balance, this analogy is applicable to why it is necessary to optimize each processing stage (a stone) in the finishing of cellulosic fibres, in order to produce a cumulative reduction in energy and resource consumption.
The world is full of wonders. Most people know that the cheetah is the fastest land-based animal and can run up to 70 mph. But did you know that the Indo-pacific Sailfish can swim also with a speed of 68 mph too? You might be asking, how are these trivia related to the textile world and the need for reduced resource consumption?
Despite being able to move at those speeds, these animals do not always move at their maximum speed, because this is not sustainable in the long run, even in nature. Maximum power is induced only when needed for hunting or to escape.
Similarly, in the textile world, in particularly the pretreatment processes of cotton knit goods, it is not sustainable for both the environment and businesses, if our processes are always running on maximum effort to reach achieve targets.
In the following article (and more to come), we will focus on the enzymatic bio-scouring process on the cotton material as the pretreatment step for selected shades.
Studies have shown that shade distribution of leading retailers and brands indicated an approximation of 30% of colors sold, are blacks, navies, and other dark shades. A typical pretreatment process when deep shades are dyed on cotton involves a conventional scouring method which removes the natural fats, waxes, inorganic salts and heavy metals of the greige cotton.
Unfortunately, this process utilizes the almost equal amount of water and energy as conventional bleaching. The resource consumption of a 600 kg batch for a traditional scouring process, followed by conventional reactive dyeing, rinsing, and soaping, at a Liquor Ratio (LR) of 8:1, with a carry-over of 300% is approximate:
Conventional Process Route
What these textile mills can consider incorporating is “Enzymatic Bio-scouring” (at least for seed-free cotton fabrics such as knitted from combed cotton yarn). Bio-scouring, using the enzyme pectinase to remove waxes and oils from cotton fabrics, ensures good fiber wettability and can, therefore, promote consistent dye penetration and diffusion.
Here, we can recommend DyStar’s Sera® Zyme C-PE which also works well for knitted polyester-cotton blend fabrics. In all applications, bio-scouring has the added advantage of eliminating the need for the large quantities of caustic soda and acid-based rinsing agents essential for traditional scouring methods. Thus, significantly reduced water consumption, energy consumption as well as the chemical loading of effluent discharge and finally reduced process time (=higher productivity) can be reached.
When using the Sera® Zyme C-PE based bio-scouring process instead of a conventional caustic soda based scouring process, the following savings and resource efficiencies can be reached during the production of a 600 kg batch:
Sustainable Process Route through Bio-scouring
10,0 % process time (41 min)
16,0 % water (6000 liters)
11,0 % Electricity (3,9 kWh)
20,0 % Steam (0,1 tons)
The reduction in electricity and steam consumption will lead to an improved carbon food print of your production.
Click here for more information about sustainability at DyStar.