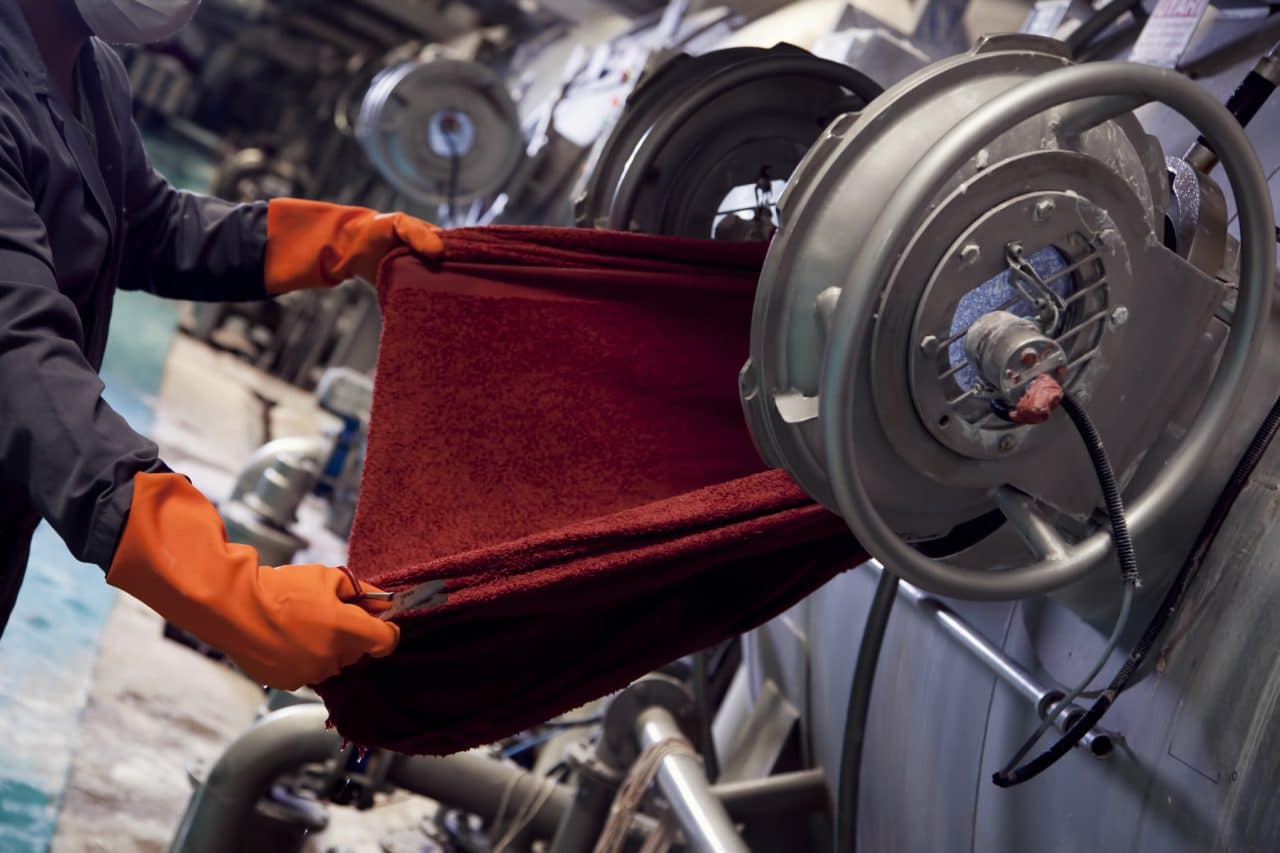
15 Dec Sustainable Color Communication: Realizing the Color Inspiration in the Supply Chain | Step 3
In the last blog post, we established that setting “a color standard” for a color inspiration, was a key step to initiating a sustainable communication process in the supply chain. Furthermore, we demonstrated that the use of a proper color standard positively impacts the planet, profit, and people by reducing waste, cost, and time.
We are now at the stage in the color communication process where the lab-dip has been approved against the color standard and the textile mill needs to reproduce the lab-dip (10 grams in size) on a production scale (1,000 kilograms in size). The scale-up factor of 100,000 significantly increases the chances of generating more waste, cost and time. However, the scale-up factor is not the main concern. The dyes and processes that are used during the production will be the key influencing factors on whether the production is sustainable or not.
How can Designers or Color Managers develop a sustainable color process at the textile mill?
Establish a color standard for the color inspiration. Communicating with garment samples adds more variables in the dying process because there are many unknowns as to how the garment sample was dyed.
Use a color standard from a color service provider that is a manufacturer of the textile dyes. This allows the designer or color manager to choose color standards produced with high-performance dyes. This provides the textile mills with a sustainable standard to follow and not re-create, which saves time and money!
Monitor the supply chain. Request the performance characteristics of dyes that are being used to color the textiles. Develop a tracking system to provide traceability.
Establish and Monitor an RSL. It’s important to avoid restricted substances from contaminating the garments. Establishing, communicating and monitoring RSLs at the textile mill will ensure that your process is sustainable.
LLow-PerformanceDyes vs. High-Performance Dyes
Let’s look a little deeper at the impact of the dyes and the dyeing processes in regards to producing a cotton T-shirt. Cotton is one of the two biggest fibers consumed globally with an expected consumption of >20 Mio. tons in 2012/20131. At this consumption level, the coloration of cotton has a tremendous global impact on the planet, profit, and people.
A common practice in the textile industry is that the textile mill takes the color standard or color inspiration (if a standard is not being used) and creates a dye recipe during that lab-dip stage that can be used to scale-up for production. The selection of dyes used at the scale-up stage will influence the sustainability of the dyeing and washing processes. For dyeing cotton, reactive dyes are most commonly used; however, reactive dyes are further classified as either Low or High performance.
The utilization of low-performance reactive dye for cotton will have a negative impact on the planet, profit, and people for 4 main reasons.
1. Low fixation – Low-performance reactive dyes, which represent the largest class of dyes used for the coloration of cotton, have a low fixation (50 to 70%) of the dye to the cotton. The low fixation results in up to half of the dye going into the wastewater.
2. Water, energy and time consumption – Low-performance dyes require longer process times to wash the unfixed dye off of the fabric. Longer process times require more water, energy and time. To color 1 kilogram of cotton with low-performance dyes requires about 70 liters of water for the dyeing and washing process. This equates to a swimming pool worth of water to dye 7,000 T-shirts (0.25 kilograms in weight)! Furthermore, the additional process time for dyeing and washing low-performance dyes is up to 2 hours, which increases the energy costs by up to 25%.
3. Wrong First Time (WFT) processing – Low-performance dyes typically result in Wrong First Time (WFT) processing. WFT means that from lab to production the processes will require additional dye to match the color standard, or the fabric will have to be over-dyed, or the fabric will have to be stripped and re-dyed. WFT processes increase the costs by 20 to 100% as demonstrated in the graphic below. As expected, additional water, energy and time are also required.
4. Ecological Controls – Low-performance dyes are typically commodity dyes manufactured by a variety of producers. Many of these manufacturers do not have good ecological controls in the production of the dyes. As a result, they may manufacture dyes that contain Restricted Substances that end up contaminating the T-shirt.
Good Ecological Contols Poor Ecological Controls
The utilization of high-performance reactive dyes for cotton will have a positive impact on the planet, profit, and people. In contrast to low-performance dyes, high-performance dyes exhibit high fixation yields on cotton (90% or greater) and excellent lab to production repeatability yielding Right First Time (RFT) processes. Furthermore, these dyes are capable of being dyed and washed with less water (50%) and shortened processes (2 to 3 hours savings). High-performance dyes use about 30 to 35 liters of water per 1 kilogram of cotton fabric or 14,000 T-shirts for a swimming pool of water!
If you are already using a color service provider like Color Solutions International and a dyestuff manufacturer like DyStar, then you are connected to the most sustainable color communication process available for designers, color managers, and product developers.
Related Posts:
Sustainable Color Communication
Supply Chain Collaboration – The new paradigm for sustainable textiles